Thousands of face shields designed by ABI researchers produced for healthcare workers around New Zealand
22 April 2020
Auckland Bioengineering Institute (ABI) and MedTech CoRE researchers have designed a re-usable face shield to help keep medical staff safe when treating patients infected with Covid-19.
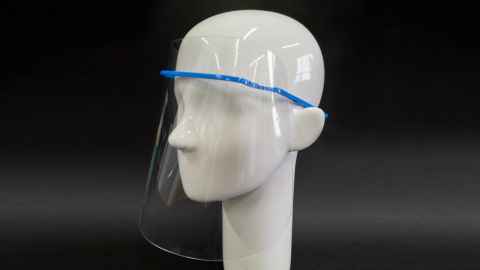
In response to demand, from both the public and private health sector, 20,000 units have been manufactured to date.
The design is simple but effective, comprised of a plastic frame and transparent plastic sheet. Importantly both components can be disinfected and reused.
It was developed by Dr Paul Roberts, a technical development engineer at the ABI with support from MedTech CoRE collaborators and industry partners. He and his team sprang into action after a meeting with local clinicians on 21 March who expressed concerns about the lack of Personal Protective Equipment (PPE) in the healthcare sector in New Zealand.
As he notes, the sector has not had to deal with infectious disease at this scale before. “Face shields are not typically held in stock as part of normal personal protective gear, so clinicians were driving to Mitre 10 and Bunnings to find something to use as face shields.”
Dr Roberts used plastic glasses deployed in the Emergency Department of some hospitals as a starting point. “By mid-March, some EDs were already seeing cases coming through, and wanted a shield that would help protect their whole face.”
The face shields provide another layer of protection, to be worn over surgical face masks, to reduce the viral load that healthcare workers can be exposed to. As Dr Roberts cautions, they “aren’t perfect”, and in an ideal situation further consultation with users would have enabled design refinements, but it was an effective response to an emerging and fast-evolving situation.
“These could also be used by people in a range of contexts, such as ambulance workers, GPs, and police,” says Dr Roberts.
The face shield was originally prototyped by laser cutting the plastic shield and retrofitting to frames of safety glasses available to some DHBs, says Dr Roberts. High and urgent demand prompted them to switch to injection moulding frames and stamping the plastic sheet.
This has allowed production volumes of 10,000 per day. They are being manufactured by Lower Hutt and Auckland factories which produce food packaging, as they have the necessarily technology and are familiar with working to high standards of hygiene.
This is just not just another example of the PPE equipment being designed and produced by DIY-ers here and around the world, says Professor Peter Hunter, director of the ABI.
“This face shield has been designed in consultation with clinical staff and is now being manufactured locally in New Zealand in sufficient quantities to be able to provide a secure supply.”
So much has been achieved in a short time, he adds. “In a little over two weeks Paul has been able to go from a prototype design to having these face shields manufactured in the thousands to meet the demand around New Zealand.”
Media contact
Margo White | Media Adviser
Communications Office
Tel 09 923 5504
Mob 021 926 408
Email margo.white@auckland.ac.nz