Mechanical and Mechatronics Engineering
Applications for 2025-2026 open on 1 July 2025
Self-powered vibration monitoring based on vibration energy harvesting
Project code: ENG004
Supervisor(s):
Discipline(s):
Mechanical and Mechatronics Engineering
Project
Vibrations impact the integrity of engineering structures and systems (e.g. machinery, rail track, wind turbine). Vibration monitoring is therefore critical for predictive maintenance. However, the existing solution of battery powered vibration sensors is constrained by the limited life span of batteries. Therefore, vibration energy harvesting gains enormous research interest as a sustainable power source for sensing and monitoring.
The role
In this project, we will develop a device integrating the vibration sensing and vibration energy harvesting modules as a self-powered vibration monitoring device. An electromagnetic energy harvester will be provided with about 10V AC voltage output and the student is expected to code with the nordic nrf 52840 microcontroller to measure the vibration signal from a MEMS 3-axis accelerometer and transmit the data through Low Energy Bluetooth (BLE) remotely to a smart phone or PC. A simple user interface should be developed to display the measured vibration signal on the smart phone or PC.
Prerequisites
Coding skills with C, software design, electronics and signal processing
Enhancing efficiency of a novel drone
Project code: ENG005
Supervisor(s):
Nicholas Kay
Discipline(s):
Mechanical and Mechatronics Engineering
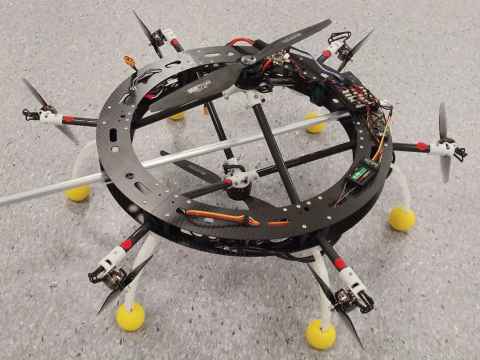
Project
The Drone Technology Research Group (dtrg.org) develops novel multirotor UAVs for outdoors and physical interaction. The most recent design uses two large central rotors. The lower of these, however, is in the wake of the upper rotor, reducing its efficicency. This project will look into improving the efficicency of this rotor by changing the blade angles of the lower rotor. This work will be conducted experimentally in the Mechatronics lab, and is suitable for Mechanical and Mechatronics students with an interest in Drones, UAVs, and Aerodynamics. There is potential for implementing any recommendations on the aircraft for flight testing within the project duration.
Improving Hardware and Software Tools for the VEX V5 Robots
Project code: ENG006
Supervisor(s):
Discipline(s):
Mechanical and Mechatronics Engineering
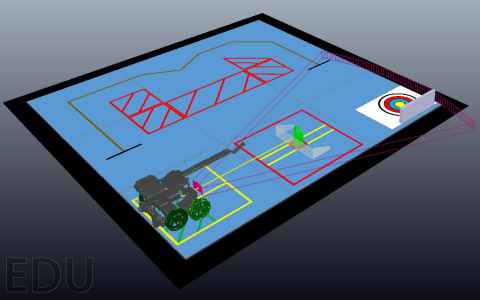
Project
This project provides an opportunity to contribute to the enhancement of the VEX V5 system utilised in MECHENG 201 for teaching robot programming and control systems concepts. The focus will be on investigating potential upgrades in hardware, software, and simulation environments to address the limitations in the current implementation.
The role
Project objectives include the evaluation and integration of new sensors, such as laser distance and colour sensors, the development of custom graphical user interfaces for the robot LCD using the LVGL library, the creation of tools for onboard data logging and analysis, and refining the existing CoppeliaSim simulation environment to support more advanced functionalities.
Participants will gain practical experience with tools such as VS Code, CoppeliaSim, MATLAB, and Excel. The project emphasises programming in C for hardware control and involves working with open-source software tools. It is open to students from all disciplines, and prior experience in MECHENG 201 is not required.
Requirements
Requirements for this project include excellent programming skills, ideally demonstrated with an A grade in MECHENG 270 or equivalent, and a willingness to learn and adapt to new tools and environments, including lightly documented open-source software.
For further details or to express interest in participating, please contact h.namik@auckland.ac.nz.
Scaling Down to Scale Up: Prototyping Mechanical Systems for Education
Project code: ENG007
Supervisor(s):
Discipline(s):
Mechanical and Mechatronics Engineering
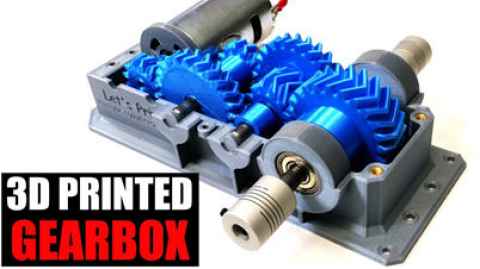
Project
This research project aims at improving a new design project developed for MECHENG 236. The goal is to develop a scaled-down, physically prototyped version of a full-scale power transmission system—comprising motors, gears, shafts, keys, bearings, clutches, brakes, and housings—using 3D printing and accessible materials.
The role
The project has two core components: engineering design and prototyping, and pedagogical research. Some proposed tasks are as follow:
- Investigate the impact of scaling and material substitutions to preserve or at least acknowledge the impact to, full-scale mechanical behavior.
- Identify aspects of the full system that are suitable to translate to a scaled down functional model, suitable for hands-on student interaction. These could be either be cheap modular components, or components that students could use CAD to design and 3D print.
- Order/aquire or CAD and print components, and assemble and test.
- Evaluate the educational impact of scaled physical models on student understanding of mechanical systems.
- Design and implement feedback mechanisms (e.g., surveys, interviews, observational studies) to assess learning outcomes.
Ideal student
This project is ideal for students interested and skilled in mechanical systems, design for education, and CAD design and prototyping.
Project
The Challenge
Imagine a robot that watches a video tutorial, understands your spoken instructions, and then builds complex products autonomously. You'll work with Vision-Language-Action (VLA) models—the same AI breakthroughs powering ChatGPT but applied to real-world robotics.
What you will do
- Test Cutting-Edge AI: Evaluate how well the latest large AI models can control robots for assembly tasks
- Build Real Systems: Program robotic arms to see, understand language, and perform complex assembly operations
- Pioneer New Methods: Develop metrics to measure robot learning and compare different AI architectures
- Solve Real Problems: Create case studies showing how universal AI models can tackle local manufacturing challenges
Your Tech Arsenal
- Hardware: Advanced robotic arm (UR5e), RGB-D cameras, GPU computing system, assembly workspace
- Software: Python, PyTorch/TensorFlow, ROS, OpenCV, state-of-the-art VLA models
Why This Matters
Your research could revolutionize manufacturing by creating robots that truly understand and work alongside humans. You'll gain hands-on experience with the most advanced AI and robotics technologies while contributing to the future of intelligent automation.
Perfect For Students Who:
- Excel at math and programming
- Are passionate about AI and robotics
- Want to work on technology that could reshape entire industries
- Love hands-on experimentation with cutting-edge tech
Ready to build the future of intelligent robotics?
Touch and 3D-Printing
Project code: ENG009
Supervisor(s):
Discipline(s):
Mechanical and Mechatronics Engineering
Project
We're using 3D printing to better understand how the human nervous system processes textures that contact the fingertip, and how that processing enables tactile perception. In previous work[1], we quantified fingertip sensitivity to texture using FDM (fused deposition modelling) 3D-printed test objects (ie., the objects were low-resolution).
The role
Here, we'll quantify sensitivity using resin 3D-printed test objects (ie., the objects are high-resolution). Higher print resolution allows us to make a wide range of textures, and therefore enables a more detailed investigation of the fingertip, its sensitivity, and tactile texture perception.
Keywords: engineering, neuroscience, biology, 3D printing, tactile perception
[1] McLean, C. F., Trew, D. J., & Hallum, L. E. (2023). A filter-rectify-filter model of the tactile perception of 3D-printed, texture-defined form. Annual International Conference of the IEEE Engineering in Medicine and Biology Society. IEEE Engineering in Medicine and Biology Society. https://doi.org/10.1109/EMBC40787.2023.10341026
Self-powered acoustic device for offshore applications
Project code: ENG010
Supervisor(s):
Andrew Hall
Discipline(s):
Mechanical and Mechatronics Engineering
Project
This project implies developing, building and ocean testing of a self-powered acoustic device for offshore applications, for example for emitting and/or receiving sound on ocean buoys and aquafarms.
The role
First, power requirements of the device, so that it can produce sounds of required intensity and frequency, are to be assessed. Then the corresponding hardware (microphones, speakers, control, battery) and electrical power generation method are to be selected. This will be followed by building and testing of the device if times allows.
Levitating fluid under action of high-frequency vibrations
Project code: ENG011
Supervisor(s):
Vladimir Yotov
Discipline(s):
Mechanical and Mechatronics Engineering
Project
The project implies experimental studies of anti-gravity phenomena arising in fluids under action of high-frequency vibrations. Several such phenomena have been previously observed experimentally, for example, the inverted pendulum becoming stable under action of vertical vibration and sinking of gas bubbles in a vertically vibrating fluid volume.
The role
The aim of this project is to build an experimental setup and make videos that can showcase one (or several) of such anti-gravity phenomena. The phenomenon of a levitating fluid under action of high-frequency vibrations, when a layer of fluid becomes suspended in air due to applied vibrations, is of particular interest.
Understanding speech across different language backgrounds: a gamified approach
Project code: ENG012
Supervisor(s):
Discipline(s):
Mechanical and Mechatronics Engineering
Project
In our day-to-day spoken communication, we listen to speech in varying acoustic environments. To decipher the speech signal accurately we ignore any variations caused by the environment while picking up on important acoustic cues such as, timing and pitch.
The role
Each language employs these acoustic features differently, for example, a 'p' would sound different in English versus Spanish. In this project, we will examine how distortion from different acoustic environments affects our speech perception to understand how we decode speech in real-world environments. This project will utilise audio VR to create an application to test how we perceive different speech sounds.
The student will be working alongside members of the Communication Acoustics Lab and the Speech Research group to develop the system and conduct perceptual tests using synthesised speech sounds. If the student is competent in software programming, another aspect to the project includes gamifying the test to make it more interesting for participants.
The project will involve taking acoustic measurements, developing a software platform for testing, and conducting experiments using the platform developed.
Ideal student
Students suitable for this project should be interested in linguistics, acoustics, and VR audio technologies. Reasonable familiarity with MATLAB or Python programming/Unity is recommended.
Exploring auditiory processing distory training on second language listeners to improve listening in noisy environments
Project code: ENG013
Supervisor(s):
Discipline(s):
Mechanical and Mechatronics Engineering
Project
In learning a new language, non-native speakers often struggle with subtle differences in how speech sounds are used and perceived—especially in real-world, noisy environments. Interestingly, some of these challenges resemble those experienced by individuals with Auditory Processing Disorder (APD), where the brain has difficulty interpreting sounds.
The role
This project explores whether training methods developed for APD can be adapted to support second language learning. The student will investigate how different auditory training techniques affect non-native English speakers' ability to perceive key speech sounds.
Working alongside the Communication Acoustics Lab and the Speech Research group, the student will help design and conduct perceptual experiments, and may contribute to developing an interactive training tool.
Ideal student
Students with an interest in speech perception, second language acquisition, or applied auditory science are encouraged to apply. Programming and statistical analysis experiences recommended.
Systematic Review and Design of single cell analysis devices for Cancer Research
Project code: ENG014
Supervisor(s):
Discipline(s):
Mechanical and Mechatronics Engineering
Project
Cancer is a pressing issue in modern medicine. Lab-on-chip (LOC) as a diagnostic tool for the early detection of cancer is an emerging field in the design and development of medical devices. Combining LOC with artificial intelligence and optical detection of cancer protein is a novel approach for personalised cancer medicine applications.
The role
In this project, the summer scholar will begin to undertake a systematic literature review first on this topic and the suitable development of an algorithm required for image analysis and the design of a diagnostic device to monitor cancer cell behaviours in real time for the early detection of cancerous cells from the biopsy samples.
The research methods for this review will include the searching of Library catalogues, Search engines for key databases such as Google Scholar, Scopus, PubMed and Medline. Online databases or abstracting and indexing services provide access to journal articles, conference proceedings, reports, dissertations and other grey literature.
Tasks
The summer student will support our research team with various tasks, including literature reviews, research ethics, instrument development (survey and semi-structured interviews), and (potentially) data analysis for a mixed methods project.
Ideal student
Familiarity with both quantitative and qualitative methods and software is preferred but not essential. The student should be self-directed and intellectually curious.
Systematic Review and New Product Development Process to Design Medical Devices
Project code: ENG015
Supervisor(s):
Discipline(s):
Mechanical and Mechatronics Engineering
Project
The new product development of wearable medical devices has a wide range of potential clinical applications, ranging from arrhythmia screening of high-risk individuals to remote management of chronic conditions such as temporomandibular disorders, heart failure or sleep related disorders.
The role
In this project, the summer scholar will undertake a systematic literature review of intelligent wearable devices for heart diseases and their impact on early detection when a suitable algorithm is integrated with the sensor network.
The research methods for this review will include the searching of Library catalogues, Search engines for key databases such as Google Scholar, Scopus, PubMed and Medline. Online databases or abstracting and indexing services provide access to journal articles, conference proceedings, reports, dissertations and other grey literature.
Tasks
The summer student will support our research team with various tasks, including literature reviews, research ethics, new product development process including survey and semi-structured interviews and (potentially) data analysis for a mixed methods project.
Ideal student
Familiarity with both quantitative and qualitative methods and software is preferred but not essential. You should be self-directed and intellectually curious.
Accelerator for Laboratory EXperiments (ALEX)
Project code: ENG019
Supervisor(s):
Discipline(s):
Mechanical and Mechatronics Engineering
Project
Cars speeding along thinly sealed roads often kick up flying stones, which pose hazards for many road users. The university is developing a wireless charging system to be mounted on the bottom of electric vehicles, where it will be especially susceptible to flying stone impact damage.
The role
Existing laboratory equipment (drop towers) could not replicate flying stone impact, as they are unable to achieve the desired projectile velocity. This project seeks to develop a multi-purpose laboratory accelerator to reliably launch small projectiles of variable masses up to configurable velocities, not exceeding 33 metres per second. The accelerator will be used primarily to characterise the impact damage of wireless chargers, and later, other materials.
Key responsibilities include:
- Evaluate and select suitable propulsion and control methods.
- Design and build a prototype accelerator.
- Test the accelerator to evaluate its reliability.
Ideal student
The ideal candidate should be willing to engage in multi-disciplinary research and development. A firm commitment to laboratory safety is essential. Strong mechanical design and prototyping skills are preferred. Experience working with pneumatic or electrical hardware is sought after but not necessary.