Making the world a better place
9 December 2019
As a student, Biotechnology and Materials Engineering alumna Yaoyao Ding was inspired by her masters supervisor’s passion for the nanomechanical properties of biomaterials. Now she’s an entrepreneur making her own mark on the world.
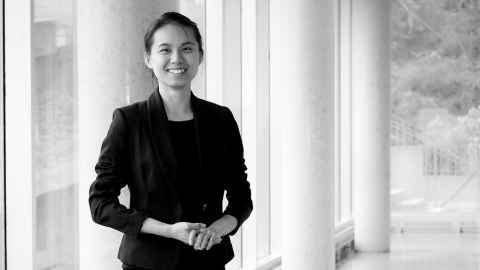
“I’VE ALWAYS BEEN interested in science and how things work. I enjoyed all the practical work and lab experiences in my degrees – it was a chance for me to be creative and make things happen.”
Making things happen and, in particular, making things, is what Yaoyao has turned her hand to in her career. After graduating from the Faculty of Science in 2008 with a Bachelor of Technology in Biotechnology, Yaoyao shifted to the Faculty of Engineering and took up a masters in materials engineering under supervisor Dr Michelle Dickinson. “From the first moment I talked to her [Michelle], I knew I wanted to become a materials engineer,” she remembers.
Yaoyao moved to Montreal, Canada, after her masters graduation, and began her PhD in materials engineering at McGill University. She then spent a year as a postdoctoral fellow at McGill, before taking a position working on additive manufacturing (AM) projects with Heroux Devtek, a landing gear manufacturer.
Additive manufacturing (also known as 3D printing) technology has revolutionised the fabrication and manufacturing industries, making the production of parts and devices simpler, quicker, and more flexible for organisations and individuals.
In 2018 Yaoyao established her start-up company, B3D Performance, which specialises in AM using metal powders and lasers.
How did you become involved with additive manufacturing?
I first became involved with AM during my postdoc at McGill University. My postdoctoral supervisor introduced me to the world of AM, which is filled with fascinating possibilities. I’ve stayed in the field ever since.
What kind of work do you do at B3D Performance?
At B3D, we work as a team. Our team specialises in AM using metal powders, and serves as a bridge between the technology and the AM technology adopters.
Through our training programmes, we help people to develop a good understanding of the benefits and limitations of AM. Through our support services, we continuously help our customers during their product development processes.
Recently, we’ve started to develop instruments to monitor the powder quality so we can reduce production costs and minimise the impact on the environment.
Why is it important for companies to be able to make their own parts? Is it just because it’s quicker and cheaper? Or is it because sometimes it’s difficult to procure the parts they need?
With AM, there’s a quicker production development cycle with the ability to prototype parts. Companies can fabricate parts on demand, which reduces their inventory, and it’s therefore easier to plan production because you have full knowledge of production capacity.
Can you tell us about a recent project or initiative you’ve worked on?
One of the challenges associated with AM is producing parts of consistent quality. In metal AM, parts are built by adding (this is why it’s called ‘additive’ manufacturing) multiple layers of metal powder, which is melted with a laser. The commercial and research communities are trying to improve the quality and reproducibility of this process.
B3D was awarded funding by the National Research Council (NRC) of Canada to develop a test tool capable of measuring the density of the metal powder bed. So far we have finished Phase I of this project and have produced a proof-of-concept instrument. We’re currently working on building the MVP (most viable product) and commercialisation. It’s really exciting.
What kind of impact do you hope your work will have?
I hope to facilitate adoption of AM into different industries, especially the aerospace, biomedical and automotive industries. I hope the machines we are building will help these industries build high quality and cost effective parts.
How do you think AM is going to change the aerospace industry in particular?
AM is going to disrupt the supply chain, and bring product designers close to the manufacturing process. I imagine we’ll see a quicker product development cycle, along with more creative part design because of the increased design freedom. A new approach to data security will also be necessary.
What has been the highlight of your career so far?
I love being an entrepreneur. I will be very proud to see my instruments hit the market and make an impact. A highlight for me has been to work with people from very different industries, backgrounds and cultures.
What drives you?
“To make the world a better place.” I love this quote from the movie Zootopia. I’m driven to help more people understand AM technology and use it to their advantage.
Finally, tell us something about yourself that we can’t learn by Googling you!
I do Latin dancing, and received a silver medal for Hustle. It’s a great way of relieving stress!
inSCight
This article appears in the December 2019 edition of inSCight, the print magazine for Faculty of Science alumni. View more articles from inSCight.
Contact inSCight.