Biomimetics Lab
ABI's Biomimetics Lab, where work on electric charge has helped create groundbreaking inventions.
Our research is centred around soft sensors, actuators and smart materials, with a special focus on dielectric elastomers. Our projects range from basic research to real world applications.
Meet the lab
We need you!
We are constantly looking for talented students for our numerous projects.
Get in touch with us for more information (i.anderson@auckland.ac.nz or masoumeh.hesam@auckland.ac.nz)
Our research
General overview
Our research revolves around combining electric charge with soft polymer to make stretch sensor for capturing gestures and body motion, actuators for soft robots, or energy converters that can transform human body motion into electricity.
Materials research and electroactive polymer actuators
Structure-Property Relationships in Nanocomposites
The past several decades has brought significant advances in the availability and variety of nanomaterials and nanoparticles. With this has come the use of nanocomposites in a diverse range of applications. Nanocomposite materials combine tiny nanoparticles with traditional engineering materials to combine the properties of the two phases into a single material. These composites often exhibit complex behaviour and multifunctionality. Much research in our lab often utilises stretchable conductive composites for many applications, taking advantage of their unique electro-mechanical properties. However, the physical mechanisms underlying their behaviour are still not fully understood.
This project uses experimental analysis, computational Monte Carlo simulation, and statistical mechanics to better understand the complex relationship between the nano to microscale structure of nanocomposites, and their emergent macroscopic behaviours.
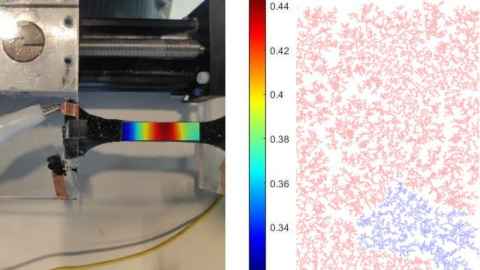
Rubber in space
Dielectric Elastomer Transducers (DETs) integrated into inflatable structures can form the basis for soft, low mass robots. These can be packed into very small spaces and then simply deployed via inflation. Being soft also makes them safer, allows them to change their shape easily to adapt to different environments and different orientations. These attributes, combined with the high power density of DETs, make active inflatables ideal for space robotics. We have constructed prototypes capable of multi-directional movement using only electrical actuation, and combined these with electro-adhesive technology to allow controllable gripping of nearby objects or surfaces. Our first design, MIDA, was presented at the EuroEAP conference of 2019. This, and our other prototypes have potential applications in the fields of on-orbit repairs, structural health monitoring (and control) of inflatable space structures, and lightweight planetary/asteroid rovers.
These prototypes face many challenges however, before they would be ready for operation in space. Low Earth Orbit (LEO, from 100 – 2000 km above the earth) is a hostile environment for any material. Any robot in LEO must contend with extreme heat (and cold), intense electromagnetic radiation, plasma, and reactive oxygen gas amongst other problems. In order to protect our soft robots, we have been developing a space-grade sunscreen, designed to shield the DETs from this harsh environment through a combination of low-Z (light metal) oxide nanoparticles suspended in a vacuum-stable silicone grease. Ground-based testing in oxygen plasma facilities is used to perform accelerated space-aging tests, simulating months to years of orbit in a matter of days. This will allow us to test how long our robots will be able to survive in space.
This project is laying the groundwork for the production of inflatable DET space robots. Though in its early stages, the development of smart-material lightweight space robots has the potential to change the ways we can explore space.
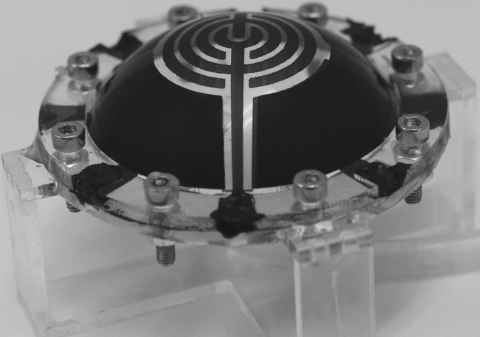
Soft transducers
Compression sensors for the manipulation of fragile objects:
The tactile sense is one of the most important ways to get information from the outside world. Take the example of babies that only use their tactile sense to find their mother in the early time after birth. In contrast, most robotic manipulators are devoid of tactile sense, which can lead to injuries or damages when manipulating soft tissues or delicate objects. We Equip a hard robotic gripper with integrated touch sensors as a distributed active skin for the very sensitive detection of contact forces, and the ability to grasp object without squeezing or dropping.
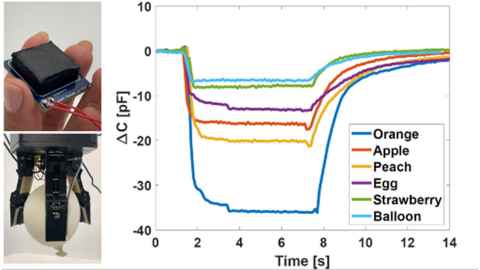
Smart sensing algorithms to extract more information from soft sensors
Soft sensors give information on how much they are being stretched or compressed by changing their capacitance? It would be extremely useful if, in addition from the amount of force or deformation applied to the sensor, we were also be able to extract location information, i.e. which part of the sensor is deformed. Instead of splitting the sensor in a multitude of sub-sensors and multiply the number of wires and electrical connections, we will rely on smart algorithm based on machine learning. The concept is simple: we send an excitation signal with a broad frequency range in the sensor, and depending on the frequency spectrum of the measured signal, we can identify not only the amplitude of the deformation, but where it has been applied. All this without any physical modification to the sensor: we rely on computing power to extract more information from simple sensors.
Consider a soft compression sensor mounted on a robotic gripper designed to handle fragile objects such as fruits or berries (figure below). From a single pair of wires, the algorithm enables to measure how much pressure is applied to the object, and where along the gripper the fruit is located.
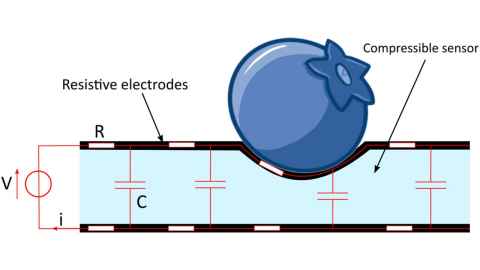
Literature on the subject:
Underwater Physiological Monitoring
We are working with hydrogels and nanocomposites to create novel soft sensors for the monitoring of human physiological signals underwater to improve diver safety. This project is funded by the Office of Naval Research.
Soft Hydrodynamic Sensing
The ocean covers most of the surface of our planet, yet much of it remains unexplored. Novel biological unmanned autonomous vehicles (BUAV) or fish-like robots aim to utilize the efficiency of undulating swimming fish like the Wahoo or the bluefin tuna to achieve longer mission times. Just like their biological counterparts, these robots require sensory input to understand the water around them to swim efficiently in flow, harvest the power of eddies and cooperate their motion with other robots.
Our research aims to create soft, robust sensors to detect hydrodynamic signatures around fish-like robots with the goal of creating sensors which can be deployed in open ocean conditions withstanding deep sea journeys. We use dielectric elastomer sensors to detect water speed, flow direction and turbulence in the water revealing objects in the flow ahead.
This project is funded by the Office of Naval Research.
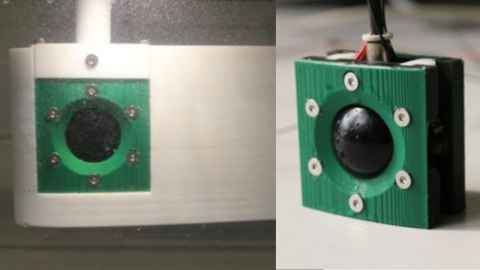
Applications
Bringing motion capture under water
Gesture recognition and sensor-based motion capture have been growing areas of research for the past few decades. With project ROADMAP (Robot-Aided Diver Navigation in Mapped Environments) the Biomimetics Lab is taking this research underwater. The project sees the development of dive gloves with integrated wearable sensors and electronics to recognize hand gestures used in diving communication and convert them into acoustic messages for diver-diver communication. The gestures can also be interpreted as commands for underwater robots.
Diver safety is of great importance, which is why knowing what the diver is doing all times would benefit underwater operations. We have developed a wearable garment that can monitor diver kinematics and infer what activity they are doing.
The video below shows an underwater trial, where a Biomimetics Lab glove is being used to communicate and command an autonomous underwater vehicle (AUV) developed by the LABUST Lab from the University of Zagreb, Croatia. As the diver performs a gesture, it is recognized and communicated to the AUV as a movement instruction.
You can find other videos on our YouTube channel:
This work is supported by the US Office for Naval Research.
Derek is working on this project and are supported by the Office of Naval Research (ONR) Global, through project ADRIATIC.
Haptics
Lightweight haptic feedback on a DE motion capturing glove
With the rising popularity of virtual reality, comes a need for more natural and intuitive human machine-interaction methods (HCI). One such method is using a motion capturing smart glove to enable hand-object interaction in VR/AR. However, when the user is trying to interact with a virtual object with their hand, the missing sense of tactility could negatively impact their experience.
This research aims to develop a lightweight haptic feedback system to a mo-cap glove. The feedback actuators are responsible for communicating haptic cues on different object properties, such as surface roughness, stiffness and location of touch.
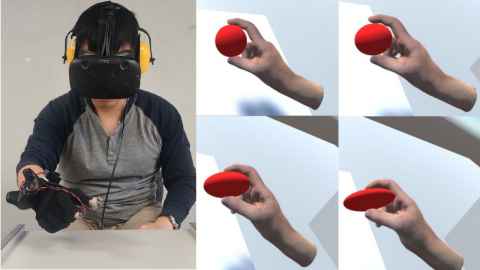
Cell stretchers
Torturing brain cells to understand traumatic brain injury
Because our soft actuators are compact, integrated to a transparent membrane and fast, they are perfect to make deformable bioreactors that can submit cells to mechanical deformation.
Why do we want to stretch cells? Because this allows to perform in-vitro experiments that are more similar to what happens in-vivo. If you think about it most of our cells are constantly submitted to mechanical deformation (muscles, cardiac cells, intestine), or force (bones), which a culture in a Petri dish cannot recreate. For example, we are using the rapid stretching rate of our actuators to submit brain cells to a mechanical insult. This enables to recreate traumatic brain injury in vitro and study gene expression or scar formation.
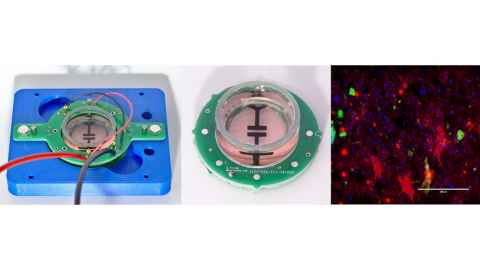
Our Spin-out companies
Members
Primary contact
Academics
Prof. Iain Anderson
Dr Masoumeh (Massi) Mahmoudinezhad
Dr Derek Orbaugh Antillon
Professionals
Gabor Papotti
Students
Arne Bruns
Cheng Huan
Sahan Jayatissa
Robin Milward
Logan Ritchie
Antony Tang
International links
- Croatia:
University of Zagreb - Laboratory for Underwater Systems and Technologies
- Germany:
Technical University Dresden - Faculty of Electrical Engineering and Information Technology
Institute of Semiconductor and Microsystems Technology - Switzerland: EMPA and EPFL
- UK: Bristol Robotics Lab
- USA:
US Army Research Lab
US Naval Undersea Warfare Centre, Newport Rhode Island